Как затачивать правильно резцы: Заточка резцов для токарного станка по металлу: видео, советы, нюансы
Как правильно заточить резец для токарного станка?
Представленное в настоящем каталоге токарное оборудование по металлу пригодно для совершения разных производственных операций. Любой токарный станок является универсальным. С его помощью можно нарезать резьбу, проделать отверстия, улучшить форму и характеристики поверхности рабочих заготовок. Для осуществления таких операций в качестве рабочих орудий применяются режущие изделия разного формата, изготовленные из стального закаленного материала.
Главными особенностями резца, определяющими его предназначение, являются основные и вспомогательные заточные углы. Заточить резец необходимо для того, чтобы привести его в функциональное состояние.
Способы заточки
Крупные предприятия, которые занимаются обработкой металлов, имеют в своем штате персонал, специализирующийся на том, чтобы затачивать резцы, для чего применяются определенные токарные станки. В небольших мастерских эти операции осуществляются силами обычных мастеров.
Чтобы заточить резец токарного станка, используются такие методы:
- абразивный – при помощи шлифовальных кругов;
- механико-химический – заключается в обработке металла определенными веществами;
- при помощи специализированного оборудования.
Заточить резец абразивным способом можно при помощи заточного токарного станка или используя только лишь шлифовальный брусок. Ручной способ не отличается высоким качеством, поскольку трудно выдержать необходимые углы. Кроме того, при разогреве металлом утрачиваются первоначальные качества, из-за чего результат будет целиком зависеть от навыков и знаний мастера.
Резцы из твердых сплавов обрабатываются посредством зеленого карборунда. Стальные рабочие элементы обтачивают с участием шлифовальных деталей вращения, обладающих умеренной твердостью.
Первоначальные операции осуществляются с применением точильных брусков, абразив которых составляет от 36 до 46, а заключительные – с абразивом в пределах 60-80. Перед монтажом элемента вращения на оборудование нужно проверить его цельность. В процессе работы шлифовальные круги иногда разламываются, нанося травмы операторам и смещая угол заточки.
Механико-химический способ отличает высокая оперативность и результативность, при этом создается идеальная по характеристикам поверхность без трещин и разломов. Метод используется для того, чтобы заточить большие резцы из твердых сплавов. Предварительно на них необходимо нанести медный купорос, обеспечивающий внешнюю защиту. Удаление вещества происходит с помощью присутствующих в нем же абразивных включений. Для осуществления данного способа пригоден токарный станок, укомплектованный вместилищем с динамичным шлифовальщиком. Зафиксированный режущий инструмент осуществляет цикличные перемещения, придавливаясь под давлением к абразивной плоскости.
Что необходимо учитывать, чтобы заточить заготовку
Режущее орудие специализированного токарного станка может перемещаться как параллельно, так и перпендикулярно центру вращения обрабатываемого инструмента резки. Станок, осуществляющий такие операции, должен предельно соответствовать производственным нормам, для чего при выборе этого оборудования необходимо учесть такие параметры:
- диаметр обработки;
- длину рабочей детали;
- интервал между центрами;
- параметры шпиндельного проема;
- мощность двигателя.
Для небольшого производства подойдут компактные настольные типы токарных станков. Цена такой техники существенно ниже оборудования для больших предприятий. При этом необходимо учитывать, что универсальность станка увеличивается пропорционально его цене. Чем дороже стоимость устройство, тем выше его функциональность.
В первую очередь нужно заточить главную заднюю плоскость, затем вспомогательную заднюю плоскость, после – лицевую поверхность и в заключение – концевое закругление.
Для получения идеальной гладкой поверхности необходимо регулярное перемещение инструмента параллельно шлифовальной плоскости. Это способствует равномерному износу и долговечности шлифовального круга.
В процессе работы резец, который нужно заточить, обрабатывают водой, чтобы снизить температуру нагрева.
Ручная доводка осуществляется:
- малозернистым оселком с применением масляных и керосиновых растворов или стальных приспособлений;
- медным кругом с помощью борного карбида и масла.
Доводка осуществляется только для резцов с кромочной шириной не выше трех миллиметров. Лучше доводить резцовый инструмент с помощью токарного станка с чугунным оселком. Это несложно и не займет много времени, зато будет существенно увеличен срок применения и повышен уровень работоспособности изделия. Кроме того, чтобы удачно заточить инструмент, необходимо четко выдерживать требуемые углы.
Правила заточки токарных резцов по металлу: инструмент, угол, доводка
Из всех технологических процедур, выполняемых над металлическими деталями, точение считается самой популярной. Ввиду этого заточка токарных резцов по металлу имеет большое значение. Ее нужно осуществлять правильно. Порядок проведения заточки токарных резцов зависит от материала, из которого сделан инструмент, назначения резца (фасонный, проходной, для нарезки резьбы, для расточки).
Как сила резания зависит от угла затачивания
Сила резания зависит от углов заточки, в особенности от переднего. Чем больше данный угол, тем меньше сила резания и тем проще отделять металлическую стружку. Однако это не означает, что передний угол возможно неограниченно увеличивать. При чрезмерном увеличении надежность резца по металлу уменьшается. Его кромка подвергается сильному износу, выкрашиванию. Ввиду этого, когда подбирают величину переднего угла, стараются не только уменьшить силу резания, но и получить прочную кромку, стойкий к износу металлорежущий инструмент.
Иногда используют токарные резцы с отрицательным передним углом (от – 5 до -10 градусов). Обычно такие инструменты используются при обточке твердых либо закаленных металлов.
youtube.com/embed/UYbW4enAFP8″ allowfullscreen=»allowfullscreen»/>
Особенности затачивания
Есть некоторые особенности, которые необходимо принимать во внимание, осуществляя затачивание резцов для токарного станка своими руками. Задняя часть инструмента обрабатывается за 3 шага:
- Сначала выполняют обработку задней части под углом, который равен заднему углу державки. Обычно он больше, чем задний угол резания (примерно на 5 градусов).
- На втором шаге осуществляют обработку задней части режущей пластинки. Ее затачивают под углом, который превышает задний угол резания на 2 градуса.
- Теперь нужный угол формируется посредством доводки. Процедура выполняется на узкой фаске, которая прилегает к рабочей кромке.
За несколько шагов затачивается и передняя часть инструмента для токарного станка. Сначала затачивание осуществляется на угол, который равен углу режущей пластинки. Угол резания, формируемый на передней части инструмента, создают посредством чистового затачивания либо доводки.
Заточка резца облегчается, если применять особые накладки, устанавливаемые промеж опорной поверхности и станочного стола. Для того чтобы точно и качественно заточить инструмент, можете изменить конструкцию стола, добавить возможность регулировать его по высоте и поворотному углу. После подобного изменения использовать накладки будет не нужно.
Для заточки резца рабочая кромка должна быть расположена на одной линии с серединой абразивного круга. Стоит принимать во внимание, в каком направлении вращается точило. Так вы сведете к минимуму шанс того, что режущая пластинка оторвётся от резцовой державки. При вращении точила пластинка должна быть прижата к державке, а не оторвана от нее.
Разумеется, что по окончании затачивания резца нужно выполнять проверку правильности исполнения. Легче всего проделывать это особым шаблоном. Можете сделать его либо купить в магазине. Если будете изготавливать шаблон собственноручно, используйте листовую сталь.
Большая твердость подобного трафарета, которую он приобретет после закаливания, позволит применять его продолжительный срок.
Для выполнения доводки применяют оселки из меди, присадочные элементы. Для доводки инструментов из твердых сплавов используют особую пасту, борный карбид, который смочен керосином. Для инструментов из иных металлов применяют оселки с малым уровнем абразивности. Их смачивают автомобильным маслом либо керосином.
Типы затачивания
Крупные предприятия, занимающиеся обработкой металлов обязательно располагают необходимыми для затачивания инструментов специалистами и оборудованием. Владельцы небольших мастерских выполняют заточку собственноручно.
Заточка резцов может быть выполнена одним из следующих методов:
- Абразивный (на шлифовочном круге).
- Механико-химический (выполняется обработка специальными средствами).
- С помощью особых приборов.
Абразивное затачивание выполняется на заточном, токарном устройстве либо на шлифовочном брусочке. Вручную трудно наточить резец, соблюдая требуемые углы. Дополнительную сложность создает нагрев металла, приводящий к потере свойств. Ввиду этого качество затачивания прямо зависимо от навыков рабочего.
Резцы из твердых сплавов точат на зеленом карборунде. Инструменты из разных видов стали проходят обработку шлифовочными кругами, сделанными из среднетвердого корунда. Начальное обрабатывание осуществляется оселками с абразивом 36-46, завершающее – 60-80. Перед тем как устанавливать круг на станочное устройство, нужно удостовериться в том, что он целостен. При обработке он может сломаться, травмировать токаря, изменить углы токарного резца.
Механико-химический способ дает возможность эффективно и быстро заточить резец, предотвращает образование сколов, трещинок. Данный метод используется для заточки больших инструментов из твердых сплавов. Они проходят обработку купоросным раствором. В результате химической реакции образуется тончайшая защитная пленка, смываемая частичками абразива, которые присутствуют в растворе. Процедура выполняется в станочном устройстве, которое оборудовано резервуаром с передвижным шлифовальником. Зафиксированный инструмент перемещается возвратно-поступательно. Кроме того, резец прижимается к абразиву (150 г на кв. см).
Заточку алмазных резцов выполняют на специальном оборудовании электрокорундовыми/кремниевыми кругами.
Углы затачивания
Далее будет приведен список углов заточки для всех распространенных материалов. Первая дробь указывает на задний угол при черновом обрабатывании, вторая – на задний угол при чистовой обработке. Третья дробь показывает величину переднего угла. В числителе указываются углы для резцов, которые точат и растачивают детали, а в знаменателе – для инструментов, строгающих заготовки.
- Сталь (твердость меньше восьмисот Мегапаскалей) – 8/6, 12/8, 15/12.
- Сталь (твердость больше восьмисот Мегапаскалей) – 8/6, 12/8, 10/10.
- Сталь (твердость больше тысячи Мегапаскалей) – 8/6, 12/10, 10/8.
- Серый чугун (твердость по Бриннелю меньше двухсот двадцати) – 6/6, 10/10, 12/8.
- Серый чугун (твердость по Бриннелю больше двухсот двадцати) – 6/6, 10/10, 8/5.
- Ковкий чугун – 8/8, 10/10, 8/8.
Основной угол в плане должен составлять 30 – 45 градусов. Ширина фаски зависит от сечения резцовых стержней.
Какие абразивные круги используются для затачивания токарных инструментов
Затачивание проходного инструмента по державке и под углом 5 градусов выполняется кругом из электрокорунда, имеющим зернистость сорок — пятьдесят, твердость СМ1/2. Окружная скорость круга составляет 25 м/с.
Подготовительное затачивание осуществляется изделиями из черного кремниевого карбида, имеющими зернистость двадцать пять — сорок, твердость М3-СМ1. Финальное затачивание отрезного инструмента выполняется кругами из зеленого кремниевого карбида, имеющими зернистость шестнадцать — двадцать пять, твердость М3-СМ1.
Параметры точильных кругов для стальных и твердосплавных резцов прописаны в таблице режимов затачивания. Там же можно посмотреть окружные скорости кручения.
В настоящее время финальное затачивание рекомендуется проводить посредством алмазного круга. В особенности это актуально для пластин из твердых сплавов. Окружная скорость круга при подготовительном/финальном затачивании не должна превышать двенадцать — пятнадцать метров в секунду.
Проведение доводки
После затачивания инструментов их доводят борным карбидом на диске из чугуна, вращающемся со скоростью 1-2 м/с. Диск должен вращаться по направлению от опоры инструмента к рабочей кромке.
При выполнении доводки лезвия и поверхности инструмента последовательно притираются. Кроме того, удаляются неровности, резцы доводятся до блеска.
Для чего проводить доводку? Дело в том, что при токарном обрабатывании инструмент изнашивается и затупляется по причине трения пластины о стружку и заготовку. Чем ровнее пластина, тем слабее трение, медленнее изнашивание инструмента.
Доводка осуществляется абразивными пастами, состоящими из борного карбида. Намочите диск для доводки керосином. Нанесите на него пасту (зигзагообразно), поднесите инструмент к диску. При использовании керосина можете применять пасту ГОИ. В случае если вы применяете современную пасту, смачивать диск керосином необязательно.
Стол подручника должен стоять так, чтобы резцовые лезвия находились чуть ниже либо на одной линии с серединой диска. Диск должен вращаться направлено к резцовой пластине.
При прижатии инструмента и выполнении доводки частички пасты измельчаются. Когда они проходят через кромки, на резце не появляется сколов, потертостей. Зерна пасты обеспечивают устранение неровностей с резцовой поверхности.
Для того чтобы более подробно изучить процедуру доводки, можете посмотреть обучающее видео. Помните, что качественно сделанная доводка обеспечит продолжительную эксплуатацию резца без повторного затачивания.
углы, станки, видео, своими руками
Технологические операции, проводимые на токарном станке с заготовками при помощи специальных приспособлений, связаны с получением в итоге изделия нужной конфигурации, представленной на чертеже. А чтобы точение было рациональным, точным необходима заточка токарных резцов по металлу, которая выполнит необходимый профиль, углы требуемой величины и соответствующие параметры рабочей части. Подготовке такого средства придается серьезное значение.
Заточка токарного резца по металлуНазначение резца, конструкция, виды
Для получения деталей из слитка металла при точении на токарном оборудовании используют специальный инструмент. Изготавливают из стали, причем твердость материала выше, чем этот показатель у обрабатываемой заготовки. Стержень-державка и рабочая головка, главные элементы конструкции резца из металла, за счет первого инструмент закрепляется на токарном станке.
Функция второй составляющей, заключается в срезании слоя поверхности металла при обработке. Стержень-державка или тело резца в сечении квадратной формы или прямоугольной. Основная режущая кромка рабочей головки в сечении фасонная (клин) иди прямая. Режущей части из металла при эксплуатации требуется регулярная заточка. В современных условиях существует достаточный выбор резцов.
Токарные резцы для обработки металла со сменными пластинами
Подбирая снасть, следует учесть такой показатель, как углы. Классификация видов выглядит следующим образом:
- проходные;
- отрезные;
- подрезные;
- расточной;
- фасонные;
- канавочные:
- фасочные;
- упорный;
Проходные, этим типом устройства обрабатывают цилиндрические болванки. Инструмент отрезного вида используют для обрезки прутков. Обрезка выполняется под заданным углом. Приспособление отрезного типа служит и для прорезания в них канавок различного назначения. Подрезные, данный тип приспособлений используют для торцевания болванок и уменьшения уступов. Расточной, это средство используют для обработки отверстий нужного диаметра в заготовках или деталях токарном станке.
Канавочный — назначение такого устройства состоит в формировании внутренних и наружных канавок на цилиндрической поверхности, выдерживая нужные углы. Иногда требуется функция отрезного типа, когда необходимо убрать часть металла заготовки. Резьбонарезные, этим устройством на токарных станках нарезают резьбу. Фасонный — предназначение этого резца состоит формировании выступов и канавок на обрабатываемой болванке, при это получаются углы с требуемыми параметрами.
Фасочные — этим устройством после заточки выполняют внутренние и наружные фаски на изделии. Упорный используют для точения деталей из металла с уступами небольших размеров. Для снижения вибрации при работе на токарном станке требуется выверять его положение. Упорный применяют для нежестких деталей.
Виды резцов подразделяют еще по направлению обработки токарном оборудовании на левые и правые, по материалу, из которого они изготовлены, по способу присоединения режущей части к державке и другим параметрам.
Порядок и правила заточки инструмента
Для предупреждения появления сколов и задиров на обрабатываемых деталях, поломки и других нежелательных факторов при работе на токарном агрегате, требуется правильная заточка резца. Эта процедура выполняется при изготовлении нового или износе старого устройства. Сам процесс заточки резцов заключается в придании требуемой формы и необходимого угла затупившемуся или новому приспособлению.
Восстановить режущую часть, можно применяя специальное оборудование по металлу при достаточном уровне мастерства и знаний работника. Ведь от правильной заточки токарных резцов зависит трудоемкость и производительность. На крупных предприятиях созданы подразделения занятые подготовкой оснастки. На малых заточка выполняется токарем.
На данный момент существуют следующие способы заточки токарных резцов:
- абразивный;
- химико-механический;
- с использованием специальных приспособлений;
Углы заточки в зависимости от вида точения стали и чугуна
Абразивная заточка резца выполняется на специальном заточном агрегате или стандартном наждаке. При использовании последнего варианта трудно выдержать нужные углы при обработке приспособления. Агрегаты для заточки имеют два круга. Абразив из белого электрокорунда используют для точения резца из быстрорежущей стали. Заточка устройств из твердых сплавов выполняется кругом из карбида кремния зеленого цвета.
Алмазным диском делают финишную шлифовку на токарном или другом агрегате. Химико-механический способ подразумевает точение в специальном составе. Точность заточки проверяют шаблонами.
Заточка резцов
Часть седьмая. Заточка токарных резцов по дереву. До этого фотообзора я никогда не затачивал токарных резцов по дереву.
В далекие школьные годы, на уроках труда в столярной мастерской, у меня были попытки
поточить проходной резец на бруске, но, как смутно помнится, мне это тогда не удалось
Как заточнику с некоторым стажем мне оказали кредит доверия и выделили под эксперимент несколько дорогих, на мой взгляд, резцов «Made in Austria».
Еще несколько подопытных резцов попроще остались за кадром.
В этой части я не буду поэтапно описывать процессы заточки.
Все это уже есть в многочисленных инструкциях к станку и приспособлениям на бумажных носителях и DVD.
Я постараюсь лишь поверхностно показать возможности Tormek в работе по заточке инструментов для резьбы по дереву.
Итак! «Галопом по Европам!»
Мне кажется, что Tormek проектировался в первую очередь для заточки всевозможных инструментов по дереву.
В подтверждение сему перечислю все то, что разработано шведами для этих целей.
Это оправка для небольших резцов по дереву SVS-32.
Но иногда ее можно использовать и для более крупного инструмента.
Очень простая в применении!
Многофункциональная оправка SVS-50 предназначена прежде всего для заточки плоских, токарных резцов с прямыми и со скошенными режущими кромками.
Имеет сменную сердцевину, повышающую ее универсальность.
Может применяться для заточки полукруглых резцов и долот с прямой режущей кромкой.
Многофункциональная оправка SVD-185.
Разработана для затачивания полукруглых токарных резцов с радиусной режущей кромкой.
Устройство настройки TTS-100. Я назову его проще и короче – калибр.
Это приложение к SVD-185 и SVS-50.
Служит для настройки процесса заточки по строго заданным (правильным)
параметрам. Т.е., если ваш когда-то новый резец после многочисленных заточек стал больше походить на чапельник, то с помощью TTS-100 вы можете все реконструировать.
Вид с другой стороны. На самом деле все не так сложно, как кажется на первый взгляд.
Для доводки внутренней стороны режущей кромки у Tormek есть приспособление LA-120. Оно представляет собой два кожаных диска. Торец большого диска имеет радиус 3 мм, а торец малого диска под углом 45 градусов – для доводки V-образных резцов и штихелей.
Эти два диска собираются с помощью оси в единую конструкцию, которая накручивается на рабочий вал Tormek со стороны кожаного круга.
Начну с самой сложной на вид, но простой в применении, оправки SVD-185 и массивного
полукруглого токарного резца радиусной режущей кромкой.
Делаю фиксацию в оправке, как показано на фото.
Точить я буду «правильно», т.е. по заданным параметрам. Поэтому при помощи калибра TTS-100 я делаю строго определенный для данного вида резца вылет из оправки SVD-185.
На самой SVD-185 есть регулятор с делениями от 0 до 5. Для данного резца необходимо выставить положение 0. (Можно разглядеть на предыдущем фото)
С помощью того же калибра TTS-100 выставляю необходимое для затачиваемого резца положение суппорта относительно остаточного диаметра круга. Фиксирую суппорт в его горизонтальных направляющих стопорными винтами.
Перед заточкой, на выключенном станке, можно визуально проверить правильность настроек. Если все верно, то РК резца в затачиваемом положении должна довольно плотно прилегать к рабочей поверхности абразивного круга.
Включаю Tormek. Если необходимо, делаю рабочую поверхность более грубой при помощи двухстороннего камня SP-650.
Надеваю SVD-185 отверстием на суппорт и начинаю заточку.
Амплитуда рабочих движений такого резца во время заточки составляет почти 180 градусов.
Аналогично выполняется чистовая заточка с применением двухстороннего камня SP-650.
После чистовой заточки переворачиваю суппорт на 180 градусов, надеваю на него оправку с зажатым в ней резцом. Регулирую вылет суппорта из горизонтальных направляющих так, чтобы РК резца плотно прилегала к поверхности кожаного круга.
Обмазываю рабочую поверхность кожаного круга абразивной пастой PA-70, делаю доводку внешнего радиуса РК резца.
После доводки на кожаном круге ослабляю зажимной винт и вынимаю из оправки резец.
Начинаю доводку внутреннего радиуса РК резца на кожаном диске LA-120 с радиусом на торце 3 мм.
Для этого суппорт можно выставить в более удобное положение.
Во время доводки «на коже» заусенец должен быть убран по всей длине РК.
На этом фото показан резец до заточки.
На этом фото резец после заточки.
Здесь я вынужден признаться, что получил не тот результат, который ожидал.
Визуально заточка резца изменилась, хотя в средней части РК угол заточки остался
прежним.
Может австрийцу не по нраву шведские параметры?
В этом вопросе мне еще предстоит разобраться. Для этого надо будет обратиться к
опытным столярам.
Аналогичным способом затачиваю другой токарный резец.
Только в этом случае я «настроился» вручную, а угол заточки «поймал» при помощи
черного маркера, как описывал ранее.
Фото резца до заточки.
Фото резца после «черновой-чистовой» заточки и доводки на кожаном круге и диске LA-120.
Еще пример. Фото до заточки.
Фото после заточки доводки.
И еще пример. До…
После…
И последний раз. До…
После…
Так выглядит токарный резец, зажатый в эту оправку SVS-50.
Здесь тоже можно задать жесткие параметры заточки при помощи калибра TTS-100,
но, я боясь, как бы опять чего не вышло, решил пойти по надежному пути ручных настроек.
С помощью некоторых премудростей выставляю правильное положение РК затачиваемого резца по отношению к рабочей поверхности абразивного круга.
Затем с помощью черного маркера методом подгона выставляю необходимый угол заточки. Для этого надо отрегулировать положение суппорта в горизонтальных направляющих Tormek. Регулировочная гайка суппорта здесь хорошо помогает.
Сделав необходимые настройки и закрепив суппорт стопорными гайками, я начинаю работу. Но перед этим поверхность абразива должна быть подготовлена для «черновой» заточки.
Аналогично выполняю заточку противоположной стороны РК резца.
После «чистовой заточки» делаю доводку РК на кожаном круге LA-220
с применением абразивной пасты PA-70.
Но перед этим необходимо перевернуть суппорт на 180 градусов и
настроить плотное прилегание РК резца к кожаной поверхности круга.
Фото резца до заточки
Фото резца после заточки
Еще один резец до заточки
После заточки
И еще один до…
и после…
В моем распоряжении не было маленьких резцов по дереву. И я не смогу в полной мере показать оправку SVS-32 в деле.
Я пошел на некоторую самодеятельность и применил SVS-32 для заточки довольно крупного токарного резца.
Так выглядит SVS-32 в работе.
Необходимый угол заточки резца я выставил методом подгона, т.е. выставил нужное положение суппорта в горизонтальных направляющих.
Фото резца до заточки.
Фото резца после заточки.
Доводку РК этого резца я выполнял в зажатом в оправку SVS-32 положении с опорой на суппорт. Суппорт я перевернул на 180 градусов и отрегулировал его вылет так, чтобы затачиваемая поверхность резца плотно прилегала к поверхности кожаного круга.
С помощью SVS-32 я умудрился заточить небольшой полукруглый резец для токарных работ.
Уже после, из инструкции, я понял, что такой резец (радиусная РК) должен затачиваться в оправке SVD-185.
Но у меня получилось!
Вот фото.
У меня было немного времени для изучения данных устройств, но пару недостатков я всё же выявил.
Первый из них заключается в том, что токарные резцы должны быть богатыми на сталь.
Т.е. сама стальная часть резца должна иметь достаточную длину вылета из рукояти.
Если сам резец представляет собой некий «огрызок» торчащий из рукояти, то заточить его на Tormek будет проблемно или даже невозможно.
Второй недостаток касается больше приспособления SVS-50 и плоских резцов с прямоугольной формой сечения.
Если эта самая форма сечения не прямоугольник, а трапеция или параллелограмм, то корректно закрепить этот резец в оправке SVS-50 не удастся, как в прочем и корректно заточить резец.
Но эта проблема решаема. Необходимо придать «телу» резца перпендикулярные формы, заодно снять фаски по всей длине.
Нужен хороший наждак и умение корректно на нем работать.
Для многих людей с «Ганзы» этого не занимать…
Круги для Т7; Т4; Т3 можно приобрести здесь: www.grinder-man.ru
Заточка токарных резцов по дереву.
Однажды ты встанешь рано утром и пойдёшь в свою мастерскую. Поставишь заготовку в токарный станок. Возьмёшь резец и начнёшь точить, но не сможешь! Возьмёшь другой резец, потом ещё один, но не сможешь работать ни одним из них. Или эта работа будет похожа на ад! Все потому что резцы затупились и больше не режут. А у тебя нет ничего, на чем можно было их заточить :(.
Если Вы начинающий токарь, то эта статья как раз для Вас. О том как точить резцы, когда точить и на чем точить.
Если Вы собираетесь активно работать на токарном станке, ты Вы сразу должны позаботиться о том, на чем и как Вы будете заправлять свои резцы. Вам понадобиться не только приобрести себе заточной станок, но и научиться правильно затачивать резцы. Обычно практика обучения работы на токарном и практика заточки резцов проходит одновременно. И ошибки вполне ожидаемы как в технике работы резцами, так и в их заточке.
Обычно у начинающих токарей популярны три основные ошибки — это перегрев рабочей части резца, заваливание режущей кромки и изменение геометрии резца.
1 Перегрев. Рядом с Вашим заточным станком всегда должна стоять емкость с водой (если это не точило с водяным охлаждением). Но не для того, чтобы раскалённый до красна резец с шипением опускать в воду, а для того чтобы предупреждать нагрев железки.
Дело в том что у резца из обычной углеродистой стали есть температура перегрева, после которой кромка резца теряет свои свойства, то есть становится хрупкой. При работе таким резцом его режущая часть быстро тупиться и на ней появляются невидимые взгляду сколы и трещины.
Такой резец необходимо переточить, убрав полностью перегретую часть.
У резцов с маркой стали HSS температура перегрева выше, но даже пройдя точку перегрева такой резец не теряет своих механических и физических свойств. Главное, при перегреве не окунать резец в воду, а дать ему остынуть на воздухе.
Главное правило здесь — как можно чаще при заточке давать резцу остынуть. Смачивать водой перед контактом с камнем или лентой и как только вода испариться, снова опускать в воду.
2 Заваливание режущей кромки. Это распространённая ошибка, после которой резец перестаёт резать. Такое происходит когда токарь затачивает свой инструмент «с рук». То есть не использует приспособления для заточки.
На самом деле старые токари по дереву всю жизнь затачивали с руки. Но для того чтобы научиться так затачивать нужны годы.
Если присмотреться к резцам старых токарей, фаска их резцов всегда полукруглая. Это неизбежно возникает при регулярной заточки с руки. Работать с таким профилем резца может только сам старый токарь, но даже ему приходиться время от времени перетачивать профиль на более грубом камне.
Гораздо правильнее для начинающего токаря потратить время и создать приспособления с которыми Вы сможете сохранять угол заточки инструмента.
Тоже самое характерно и для следующей распространённой ошибки.
3 Изменение геометрии режущей части резца.
Если Вы только начинаете осваивать обработку дерева на токарном станке, то Вам необходимо для успешного обучения создать следующие условия: правильная техника работы, острая кромка и стабильность профиля резца.
Если Вы начнёте затачивать свои резцы без приспособлений, то после каждой такой заточки Вы будете иметь совершенно другой резец, так как изменится профиль заточки. И к нему Вам придётся привыкать заново. А для новичка это ещё один вопрос — почему у меня не получается? Вам будет казаться что куда то пропала Ваша техника, хотя на самом деле Вы работаете уже другим инструментом.
В одной статье невозможно рассказать о всех нюансах касаемых заточки резцов. Поэтому ждите продолжения.
С уважением Андрей Громов.
Похожие публикации
10 полезных советов как продавать свои работы через интернет.
Этот вопрос, я думаю волнует многих любителей токарной обработки дерева и не только их. У меня есть не только опыт изготовления токарных изделий, но и их реализации. И в этом посте я опишу несколько, на мой взгляд, полезных советов по продажам…
ПодробнееВаза “Атлантида”.
Два лета подряд в Москве и Московской области бушевали ураганы.
ПодробнееШквальный ветер ломал билборды и рвал провода, обламывал ветки и валил целые деревья…
Сегментная шкатулка из красного дерева.
Эта красная шкатулка, похожая на НЛО сделана в технике сегментного точения. Я ее делал несколько лет назад…
Подробнее
Токарные резцы
Важнейшим условием хорошей работы станка является правильный выбор режущего инструмента — токарного резца — и придание ему надлежащей формы, иначе говоря — правильная заточка его. Употребление резца неподходящей для данной работы формы, а тем более — тупого или неправильно заточенного, влечет за собой в лучшем случае непроизводительную потерю времени, а зачастую и поломку резца или брак обрабатываемого изделия. Это верно в отношении не только токарных резцов, но всех режущих инструментов вообще. Поэтому, приступая к работе на станке, необходимо иметь совершенно ясное представление об основных условиях успешной работы инструмента, а также о том, как и какие грани его надо затачивать.
1. Токарные резцы. Основы процесса резания металлов
Условия высокой производительности механического режущего инструмента
Действие режущих инструментов, применяемых на станках по металлу, в частности — токарных резцов, зависит от трех главных условий: 1) от устойчивости обрабатываемого изделия, т.-е. от прочности материала его и способа закрепления его на станке; 2) от прочности инструмента, иначе говоря, от размеров его и способа закрепления; 3) от формы режущей части инструмента.
Надлежащая устойчивость и прочность станка также, конечно, необходимы.
Работающему на станке обычно приходится самому затачивать и устанавливать требуемые для работы резцы, а потому он должен быть хорошо знаком с требованиями, предъявляемыми к ним.
Токарные резцы
Кованные токарные резцы
- Подрезной резец (на рисунке — правый) применяется для торцовой (лобовой) обточки. Имеет боковой и передний зазор.
Режущее ребро затачивается под таким углом, чтобы резец не задевал заднего центра станка при приближении к центру обтачиваемой поверхности. Резец имеет лишь поперечный уклон. Продольного уклона нет.
- Остроносый резец (на рис.— правый) в настоящее время применяется редко, так как вытеснен «нормальными» резцами Тэйлора.
- Изогнутый остроносый резец (на рис.— левый). Концы резцов большинства типов часто отгибаются вправо или влево. Для некоторых работ, напр., для обработки заплечиков, это представляет удобство.
- Нормальный проходной резец. Этот тип резца выработан Тэйлором в результате многолетних опытов, показавших, что такая форма резца является наиболее выгодной для обточки. Средний продольный уклон 8°, средний поперечный уклон 14°. В дальнейшем этот резец для краткости называется „нормальным».
- Отрезной резец. Подробно рассмотрен в §§ 147 и 148.
- Круглоносый резец. Режущее ребро закруглено по произвольному радиусу, что отличает его от нормального резца.
Применяется для проточки полукруглых канавок, галтелей (выкружек), заплечиков и т. под.
- Резец для латуни. Затачивается, как резец типа 6, носок которого закруглен по малому радиусу. Не имеет ни продольного, ни поперечного уклона, во избежание врезания резца в мягкую латунь.
- Широкий отделочный резец. Очень полезен для выверки передних центров и обточки коротких конусов. Применяется часто при крупной подаче для снятия самой тонкой чистовой стружки с чугуна. Продольного уклона не имеет.
- Пружинный резец. Для обточки широких заплечиков и др. фасонных работ, где требуется снимать широкую стружку, а также для чистовой отделки чугуна и стали (с водой) Когда этот резец пружинит, режущее ребро его отходит от обрабатываемой поверхности.
- Плоский (тупоносый) резец. Очень удобен для лобовой обточки торцов большого диаметра, когда требуется снять много металла. Подача от окружности к центру. Применяется также для чистовой обработки стали, при крупной подаче и малой глубине резания («тонкой стружке»).
Для самой чистой отделки — охлаждение водой с содой. Имеет только продольный уклон, поперечного нет. Боковой зазор — с обеих сторон, следовательно, может работать как правый и как левый резец.
- Центровочный резец (резец-сверло). Затачивается под углом 120°— соответственно углу вершины спирального сверла. Работает аналогично перке. Зазор обоих режущих ребер направлен в противоположные стороны. Применяется для наметки центра отверстий, которые должны быть просверлены спиральным сверлом.
- Резец для нарезки винтовой резьбы. Носок его затачивается точно по профилю резьбы. Подробно — см. гл. 16,
- Резец для расточки. См. § 162.
Токарный станок применяется для весьма разнообразных работ — для обточки, нарезки резьбы, расточки отверстий и т. д., причем для каждой операции требуются резцы особой формы. На фиг. 62 изображены различные типы кованных токарных резцов. Впрочем, в последнее время они постепенно вытесняются более экономичными резцами небольших размеров, вставляемыми в специальные державки (см. фиг. 66).
Основные принципы, лежащие в основе выбора углов заточки резца, углов зазора и пр., изложенные в дальнейших- параграфах, являются общими для всех режущих по металлу инструментов. Тот, кто знает, почему токарный резец затачивают так, а не иначе, знает, почему выбирают определенные углы уклона и т. д., и умеет держать резец во время заточки на шлифовальном круге, быстро научится правильно затачивать и другие инструменты и поймет, какую форму они должны иметь.
Материал, из которого изготовляются резцы, должен быть достаточно тверд и вязок, чтобы противостоять усилиям, действующим на резец во время резания. Поэтому режущий инструмент по металлу изготовляют из стали, закаливают и затем отпускают.
Угол заострения резца
Действие каждого режущего инструмента аналогично действию клина, который раздвигает частицы материала. По отношению к резцам угол клина, образуемого его гранями, называется углом заострения резца или, короче, — углом резца (см. фиг. 63).
Чем тверже обрабатываемый материал, тем прочнее должно быть лезвие резца, т.-е. тем больше должен быть угол его заострения. Угол резца, подходящий для дерева, не годится для обработки железа или стали, так как величина его скоро изменится вследствие того, что режущее ребро закруглится («сдаст») под действием большого сопротивления металла резанию. Для резцов по металлу угол заострения делается от 60° до 80°, в зависимости от твердости обрабатываемого металла.
Углы зазора
Действие резца, снимающего с металла стружку, похоже на действие ножа, которым снимают кожуру с яблока. Снимаемая стружка трется об одну из граней, образующих клин, между тем как другая грань не должна касаться изделия и поэтому составляет с ним некоторый небольшой угол, т. наз. угол бокового зазора (фиг. 63). Этот угол не должен быть, вообще говоря, больше 6°, так как при увеличении его уменьшается угол резца, следовательно, резец придется чаще затачивать.
Действие силы сопротивления резанию на токарный резец направлено по касательной к окружности обтачиваемого изделия в точке соприкосновения резца с изделием (см. фиг. 64). Так как вершина — т. наз. носок — резца обычно устанавливается на высоте линии центров или несколько выше ее, то для того, чтобы не было трения между изделием и передней гранью резца, этой грани дают некоторый уклон. Угол между передней гранью и направлением резания называется углом переднего зазора или, короче, углом зазора. Обычная величина его—около 10°. Впрочем, она зависит от высоты закрепления резца в суппорте.
Углы уклона режущей грани
Для того, чтобы получить требуемый угол заострения, необходимо сточить верхнюю (режущую) грань резца так, чтобы она имела одновременно продольный уклон — от режущего ребра назад — и боковой уклон — от режущего ребра в сторону, противоположную подаче. Иначе угол заострения резца получится недостаточно острым. Уклон от носка резца назад называется углом продольного уклона режущей грани, а боковой уклон — углом поперечного уклона ее (фиг. 65). Величина этих углов зависит, естественно, от того, какой угол заострения требуется, так как чем больше уклон, тем меньше угол резца, т. -е. тем острее режущий клин, образуемый его гранями. Для обточки чугуна и инструментальной углеродистой стали угол резца должен составлять в среднем около 70°, для мягкой поделочной стали — 60°. При заточке резца сначала снимают угол зазора, затем углы уклона, с таким расчетом, чтобы получить требуемый для обработки материала угол заострения.
По сравнению с сталью латунь является металлом мягким и поэтому для обработки ее не требовалась бы придавать резцу такой же большой угол заострения, как резцу по стали. Однако, в действительности на резцах по латуни обычно углов уклона не затачивают, так как острые резцы имеют стремление «въедаться», т.-е. углубляться в мягкий материал.
Державки для резцов
Резцы из быстрорежущей стали работают примерно вдвое производительнее резцов из углеродистой инструментальной стали. Поэтому в последнее время токарные резцы, а также и другие режущие инструменты для обработки Металлов, изготовляют преимущественно из быстрорежущей стали. Так как она значительно дороже углеродистой, то широкое распространение получили различные державки, в которых надежно закрепляется небольшой кусок быстрорежущей стали, заточенный соответствующим образом. При этом получается экономия не только на стоимости стали, но и на расходах по отковке резцов.
На фиг. 66 показано несколько распространенных типов державок для резцов. На фиг. 67 представлены справа — вставные токарные резачки (пластины) из быстрорежущей стали, заточенные для разных работ, слева — работа этих резачков, закрепленных в державки.
Заточка резцов
Правильно заточенный резец при работе в нормальных условиях остается острым в течение довольно долгого времени. Как только он обнаружит признаки затупления, необходимо немедленно переточить его, иначе пострадает не только резец, но и обрабатываемое им изделие. Тупой резец не столько режет металл, сколько вырывает частицы его, поэтому обрабатываемая поверхность не может получиться гладкой. Одним из основных факторов производительной работы станка является остро заточенный резец.
Нужно помнить, что неправильная заточка резцов ложится тяжелым бременем на стоимость изделий уже одной только стоимостью излишне сношенного материала резцов и точильных кругов. Где надо затачивать резец — сверху, спереди, сбоку или со всех сторон понемногу? Дать определенные правила на этот счет нельзя, и при заточке резца следует исходить из того, для какой работы он предназначается. Способ заточки в большой степени зависит и от того, сколько времени должен работать резец без переточки и сколько времени всего он должен служить.
Затачивая резец из углеродистой стали, не следует слишком сильно прижимать его к точильному кругу, так как иначе режущее ребро нагреется (обычно оно принимает при этом синий цвет) и отпустится, т.-е. пропадет его закалка. Предпочтительнее пользоваться мокрым точилом. Резцы быстрорежущей стали теряют закалку не так легко, но иногда, при недостаточном количестве воды на поверхности их появляются трещины. Поэтому, во-первых, не надо жалеть воды, во-вторых — не следует чересчур сильно нажимать на резец во время заточки.
Не держите резец на одном месте, перемещайте его так, чтобы он прижимался к разным местам цилиндрической поверхности круга. При этом резец надо постепенно поворачивать, как показано на фиг. 68, т.-е., чтобы он принимал последовательно положения a, b, c.
Малые резцы не следует затачивать в державках, потому что, во-первых, это неудобно, во-вторых, можно одновременно сточить и конец державки. На фиг. 69 показано, как надо держать такие резцы во время заточки.
Начинающему рекомендуется попрактиковаться сначала на маленьких кусках простой поделочной стали подходящей формы и только потом перейти к заточке вставных резцов быстрорежущей стали. Вначале получение заточкой правильного заднего угла на таком резце представляет некоторые затруднения, так как для работы резец вставляется в державку под известным углом. Поэтому в первое время, пока нет навыка, лучше всего пользоваться шаблоном. В тех случаях, когда требуется получить задний угол в 10°, удобно пользоваться шаблоном для токарных центров (см. фиг. 85), угол которого 60°, так как в большинстве державок резец закрепляется так, что верхняя грань его составляет 20° с горизонталью (фиг. 70). Если угол резца отличается от 60°, нетрудно вырезать соответствующий шаблон из куска листового металла.
Чего не следует делать при заточке резца
- Не затачивайте резец наугад; отдавайте себе отчет в том, где и сколько металла надо снять.
- Держите резец крепко и уверенно.
- Не прижимайте резец к кругу с левой руки; держите его надлежащим образом, это и легче всего.
- Не жалейте воды.
- Не держите резец все время на одном месте шлифовального круга, иначе вы прорежете канавку на нем.
- Не пользуйтесь, если это возможно, таким кругом, который потерял правильную цилиндрическую форму или поверхность которого сильно выщерблена.
- Не затачивайте резец на торцевой поверхности круга, если в этом нет необходимости: когда понадобится точить на торце, его поверхность будет уже не плоской, а исцарапанной вами или кем-нибудь другим.
- Не опирайте вставные резачки на подручник: держите их в левой руке и на подручник опирайтесь рукой.
- Не отодвигайте подручник дальше, чем на 1,5—2 мм от шлифовального круга.
- Не закругляйте вершину резца для нарезания резьбы и не превращайте, наоборот, резец с закругленным носком в резец для нарезки резьбы: это напрасная трата материала и времени.
2. Скорость резания, скорость подачи и глубина резания
Определения скорости резания, скорости подачи и толщины стружки
Скорость резания всякой операции, состоящей в снятии стружки или в разрезании металла, выражается в метрах в минуту или миллиметрах в секунду. Для токарных станков скорость резания равна длине, проходимой цилиндрической (при цилиндрической обточке) или торцевой (при лобовой обточке) поверхностью изделия в единицу времени по лезвию резца. Если бы можно было точно измерить длину стружки, снятой резцом в течение минуты (или секунды), она представила бы скорость резания.
Скоростью подачи или просто подачей (питанием) при обточке называется величина перемещения резца вдоль обрабатываемого предмета за один оборот последнего. Если, например, при обточке вала подача составляет 0,5 мм, то это значит, что когда изделие сделает 100 оборотов, суппорт передвинется на 0,5 х 100 = 50 мм. Часто употребляют выражения: «большая» или «крупная» подача, „малая» или „тонкая» подача. Эти выражения имеют смысл только в том случае, когда говорят о станках приблизительно одинаковой мощности. Понятно, что одна и та же подача может быть „малой» для крупного станка и „большой» для станка малой мощности.
Глубиной резания называется толщина слоя металла, снимаемого резцом; так называют иногда и толщину снимаемой стружки, хотя эти величины не вполне одинаковы вследствие деформирования металла при резании. Положим, например, что требуется стальную болванку диаметром 50 мм обточить на токарном станке до диаметра 47 мм с одного прохода. Ясно, что глубина резания должна быть (50 — 47) /2 = 1,5 мм.
Элемент времени
Одним из основных факторов, определяющих производительность машины или мастерской, является время. От скорости, с которой металл снимается с изделия, зависит время полной обработки его. Количество снимаемой стружки зависит, в свою очередь, от трех элементов — глубины резания, величины подачи и скорости резания. Рассмотрим для примера токарную работу.
- Предположим, что требуется уменьшить диаметр изделия с 50 мм до 47 мм, т.-е. глубина резания должна быть 1,5 мм. Если резец может взять такую стружку с одного прохода, то нет никакого смысла делать два прохода, снимая стружку в 0,75 мм, так как при этом обточка потребовала бы вдвое больше времени. Следовательно, первым фактором производительности является глубина резания.
- Если при одном обороте изделия резец подается на 0,4 мм, в то время, как можно было бы сообщить ему подачу в 0,8 мм, то для прохода определенной длины потребуется вдвое большее число оборотов изделия, иначе говоря, при прочих равных условиях, вдвое больше времени.
Таким образом, величина подачи является вторым фактором, влияющим на скорость обработки.
- Пусть диаметр изделия 50 мм и число оборотов его 65 в минуту. Скорость резания составляет очевидно: π ✖ 0,050 ✖ 65 = 10 метр в минуту. Если резец может работать (без ненормально частой переточки) со скоростью резания 20 метр/мин, то неэкономично давать шпинделю станка только 65 об мин. Следовательно, третьим фактором производительности является скорость резания.
Задача производительной и экономичной работы мастерской сводится, поэтому, к умелому подбору скорости резания, величины подачи и глубины резания для каждой работы и к выбору соответствующего станка. Удачный подбор этих элементов требует большого опыта. Проще находить их при помощи подсчета по известным формулам.
Выбор скорости резания и величины подачи
Надлежащие подача и глубина резания определяются таким большим числом условий, что дать твердые правила для выбора их невозможно. Форма резца, способ закрепления его, сорт стали, из которой он сделан; род обрабатываемого материала — сталь машиноподелочная (конструкционная) или инструментальная, латунь или чугун; форма изделия и способность его сопротивляться давлению резца; род обработки (черновая или чистовая), все эти обстоятельства приходится учитывать при назначении глубины резания и величины подачи.
Точно также целый ряд условий определяет необходимую скорость резания, и нет возможности составить такую таблицу, которая охватывала бы все случаи обработки. Однако, для разных металлов существуют определенные, твердо установленные опытом средние, значения скоростей резания.
Средние значения скорости резания для резцов углеродистой стали:
- Отожженная инструментальная сталь — 7,5 метр/мин
- Поделочная сталь и железо — 10.5 метр/мин
- Чугун — 12 метр/мин
- Латунь — 30 метр/мин
Скорости резания для резцов из быстрорежущей стали — по крайней мере в два раза больше.
Не следует смешивать скорость резания с числом оборотов в минуту. Скорость резания при обточке выражается формулой:
V = π Dn
где V — скорость в метрах в минуту
D — диаметр изделия в метрах
п — число оборотов в минуту
Скорость в миллиметрах в секунду v:
v = πdn /60
где d — диаметр изделия в миллиметрах
п — число оборотов его в минуту
Из этих формул ясно, что для данной скорости резания число оборотов обратно пропорционально диаметру изделия.
Очевидно, число оборотов вычисляется по одной из приведенных формул:
n = V / πD или n = 60 v / πd
где буквы имеют только что указанные значения.
Так, например, если требуется обточить латунный валик диаметром 120 мм, то выбирая скорость резания по приведенной таблице V = 30 метр /мин, получим:
n = V / πD = 30 / π 0,120 = 80 об/мин
Определение числа оборотов обычно производят только начинающие токаря. Со временем вырабатывается профессиональное чутье, позволяющее давать станку нужную скорость, почти не думая об этом.
В современных научно-организованных заводах скорость резания или число оборотов станка назначается мастером, получающим соответствующие указания от нормировочного бюро завода.
Генри Д. Бэргард Слесарное дело. Токарные станки, Книга, 1930, Москва. (Henry D. Burghardt: Machine Tool Operation, Part I: The Lathe; Bench Work and Work at the Forge, New York: McGraw-Hill Book Co.; London: Hill Pub. Co., 1919) (Книга переиздана в 2015 году издательством Andesite Press)
Читайте также: Заводы производители токарных станков в России
Связанные ссылки. Дополнительная информация
Заточка резцов для станка по металлу: способы, технология, видео
Эффективность и безопасность токарных работ напрямую зависят от вида и качества заточки используемого инструмента, во избежание ошибок важно уметь правильно его выбирать и подготавливать. В промышленных масштабах эти действия проводятся с помощью специальных станков, в остальных случаях резцы приходится заострять своими руками. Несмотря на простую последовательность, работы по заточке требуют опыта и учета многих нюансов: от материала инструмента до его типа и назначения.
Оглавление:
- Особенности
- Классификация резцов
- Технология заточки
- Рекомендации по выполнению работ и видео уроки
Конструктивные особенности токарных резцов
Этот инструмент имеет простое исполнение и состоит из двух элементов: стержня, удерживающего его в станке, и рабочей головки с режущей частью, непосредственно обрабатывающей металлы и твердые материалы и нуждающейся в периодическом затачивании. Фиксирующая часть как правило имеет геометрическое (квадратное или прямоугольное) сечение, снижающее риски проворачивания, смещения или выбивания резца из токарного станка, и вытянутую форму. Режущая часть (рабочая) отличается более сложным исполнением, она формируется из нескольких смежных кромок и плоскостей с разными углами затачивания.
Головка резца имеет 2 поверхности: переднюю, отводящую стружку, и задние стороны, обращенные к детали и разделяемые на основные и вспомогательные. Это же относится к режущим кромкам, главная из которых образуется при пересечении передней поверхности и задней основной. Углы их заточки определяют назначение резца и считаются важной характеристикой: в зависимости от месторасположения они разделяются на заострения, задние главные и такие же передние, их сумма с отклонениями от соответствующей оси резания всегда равняется 90°. Конструкцию рабочей головки резца также определяют углы между плоскостью обработки и передней поверхностью, проекциями кромок, направлением подачи и отображением главной линии реза.
Виды инструментов для токарного оборудования
Классификация резцов условная, ассортимент включает изделия с разным направлением подачи (левые и правые), конструктивным исполнением (прямые, отогнутые с отклонением оси головки влево или вправо, изогнутые, оттянутые и имеющие уникальную форму), сечением (круглые, квадратные или прямоугольные), способом изготовления (цельные и составные, с режущей частью в виде пластины) и установкой (радиальные и тангенциальные). Соответственно токарные резцы используются при разных работах: от черновых до шлифовальных, в зависимости от целевого назначения и способа обработки заготовки выделяют следующие разновидности:
- Проходные, предназначенные для снятия основной массы припуска с поверхности заготовки вдоль ее оси вращения. Как правило, их режущая часть имеет форму пластины и изготавливается из быстрорежущего металла, а стержень – из стали 45 или 50.
- Подрезные, используемые при черновой обработке деталей, точении наружных поверхностей и торцевании.
Особенностью этих резцов является наличие криволинейного профиля передней части, способствующего завиванию стружки, и фаски, упрочняющей режущую кромку. Эту разновидность изготавливают как из легированных сталей, так и из особо твердых сплавов металлов.
- Расточные, для обработки готовых глухих или сквозных отверстий, полученных путем сверления, отливки или штамповки. Эти операции считаются более сложными в сравнении с наружным обтачиванием, при выборе и заточке этой разновидности учитывается, что размер поперечного сечения токарного резца всегда должен быть меньше диаметра прохода.
- Канавочные или прорезные, относящиеся к многофункциональным, и используемые при формировании канавок на деталях со сложной конфигурацией (включая цилиндрические и конические), выполнения осевой проточки, порезки торцов и других токарных операций. Размеры и форма режущей кромки у этой разновидности подбираются исходя из ширины формируемой борозды, в зависимости от требуемой радиальности канавки их заточка бывает прямо- и криволинейной.
- Фасонные, относящиеся к нестандартным, и устанавливаемые при необходимости высокоточной обработки сложных деталей, в большинстве случаев их изготавливают под конкретные типоразмеры и формы.
- Резьбонарезные, используемые для создания с помощью токарных станков внутренних и внешних резьб с разным шагом и профилем. Они воздействуют на заготовку всеми точками кромки и совершают относительно нее винтовое движение.
- Фасочные, предназначенные для снятия фасок, чаще всего под углом в 30 и 45°.
В зависимости от материала основы и режущей части все токарные резцы разделяются на:
- Изготовленные из разных марок инструментальной стали: углеродистой (оптимальные при ведении обработки на малых скоростях), легированной (имеющие средние показатели теплостойкости и прочности) и быстрорежущей (характеризующиеся повышенной производительностью).
- Твердосплавные, используемые при высоких скоростях реза, и устанавливаемыми на токарных станках по металлу, работающими с особо твердыми и прочными заготовками или выполняющими высокоточные операции.
- Металлокерамические, представляющие собой композиты на основе вольфрама, титана, тантала или их смесей, цементируемые кобальтом.
- Минералокерамические (технический глинозем), отличающиеся повышенной теплостойкостью, но из-за хрупкости не используемые при необходимости ударных работ и массового выпуска изделий на токарном оборудовании.
- Керметовые, представляющие собой сплавы минералов, металлов и карбидов и обладающие более высокой стойкостью к механическим воздействиям в сравнении с предыдущей разновидностью.
- Алмазные токарные резцы, используемые в автоматических линиях с крупносерийным и массовым производством однородных изделий с первым и вторым классом точности, и высокой чистотой поверхностей. Эти изделия оказывают минимальное влияние на структуру материала заготовки вне зависимости от его степени твердости и не нуждаются в заточке.
- Эльборовые, представляющие собой резцы с пластинами из сверхтвердого синтетического материала.
youtube.com/embed/wogPoHjX9sM» frameborder=»0″ allowfullscreen=»allowfullscreen»/>
Правила заточки токарного инструмента, нюансы и схемы
В данной процедуре нуждаются все резцы за исключением имеющих сменные твердосплавные пластины, при отсутствии специальных станков токарь проводит ее своими силами. Среди практикуемых и проверенных временем способов выделяют:
- Абразивную заточку режущего инструмента, выполняемую на станке с шлифовальным кругом или с помощью бруса. Материал оселок подбирают исходя из твердости обрабатываемого металла или композита. Разновидности из твердых сплавов советуют заточить на зеленом корунде, из обычных сталей – на белом.
- Химико-механическую обработку, заключающуюся в нанесении на режущую кромку раствора медного купороса с последующим смывом его абразивными составами с шлифованием подвижным элементом. Такие действия позволяют качественно и быстро заточить крупный инструмент из закаленной стали и твердых сплавов с одновременным увеличением его трещиноустойчивости, способ ценится за эффективность и обеспечение гладкой поверхности.
- Заточку резцов на специализированном оборудовании со сменными или разными кругами, включая алмазные доводочные.
При выполнении работ своими руками чаще всего выбирается абразивный способ, как более доступный и простой. При его реализации придерживаются четкой последовательности действий: первой следует заточить основную заднюю грань, следующей идет задняя вспомогательная и только потом передняя. Работы завершаются затачиванием радиуса закругления, на всех этапах режущий инструмент прижимают к абразивному камню с постоянным смещением вдоль поверхности, как с целью сокращения износа круга, так и во избежание перегрева резца. Вне зависимости от вида обрабатываемой плоскости, в ходе абразивной заточки избегают как отрыва, так и чрезмерного придавливания.
Проверить насколько хорошо заточен ваш резец помогают специальные трафареты. Их можно купить или сделать самому из листа металла, вырезая в нужных местах шаблон, соответствующий ходовым линиям и углам заточки.
Впоследствии такую заготовку рекомендуют закалить и использовать как при проверке правильности подготовки резца, так и с целью оценки его состояния. Сверке подлежат все углы, чем выше требования к качеству изделий, получаемых на токарных станках, тем точнее должен быть сделанный своими руками шаблон.
Заточить инструмент на крупном абразиве недостаточно, завершающим этапом является доводка небольших участков поверхностей резца, примыкающих к его режущим граням. Для этих целей на край круглого диска наносится абразивная паста на основе борных карбидов или полировальные составы ГОИ, после чего к нему прижимается нужной стороной токарный резец и запускается процесс вращения с направленностью к пластине.
Этот этап несложно выполнить самостоятельно, при такой обработке мелкие зерна устраняют малейшие неровности, что в конечном итоге увеличивает ресурс инструмента. При доводке составами с низкой абразивностью или заточке твердосплавных резцов поверхность круга рекомендуется дополнительно намазать керосином или аналогичным веществом, при использовании современных паст или круга из меди в этом нет необходимости.
Советы
Заточка резцов для токарного станка требует постоянного внимания, для достижения оптимального результата рекомендуется:
- Охлаждать инструмент водой или делать перерывы в работе.
- Использовать для заточки станки с возможностью регулировки высоты и угла поворота шлифовального круга или размещать под них специальные подкладки. В идеальном варианте уровень режущей кромки и центральной оси точила совпадают или смещается не более чем на 3-5 мм вниз.
- Отслеживать углы заточки, абразивность шлифовального круга и скорость его вращения в зависимости от материала инструмента и вида обработки (чистовой или черновой) с помощью соответствующих таблиц режимов затачивания.
- Контролировать направление движения круга. При заточке токарных резцов своими руками основную опасность представляют отлетающие пластины, при придавливании их точилом этот риск минимальный, и наоборот.
youtube.com/embed/WkRbbd_N6YI» frameborder=»0″ allowfullscreen=»allowfullscreen»/>
Цех болторезных станков | ||||
После некоторого использования болторезных станков вы можете заметить, что на лезвиях есть небольшие вмятины и сколы, которые часто могут возникать, когда они используются для резки закаленной стали.Решить эту проблему можно, заточив их. | ||||
Вам понадобится: —
| ||||
Что такое фрезерный напильник? Напильник для фрезерования — это инструмент с абразивными зубьями, предназначенный для заточки металлических лезвий. Для получения дополнительной информации о фрезерных файлах и их использовании см .: Фрезерные файлы | ||||
Что такое угловая шлифовальная машина?Угловая шлифовальная машина — это инструмент с абразивным диском, который вращается электродвигателем. Для получения дополнительной информации об угловых шлифовальных машинах и их использовании см .: Угловые шлифовальные машины. | ||||
Если вы используете угловую шлифовальную машину для заточки болторезных станков, вам потребуется шлифовальный диск по металлу. Для получения дополнительной информации см .: Угловые шлифовальные машины. | ||||
Шаг 1.![]() Перед тем, как затачивать лезвия болторезных станков, убедитесь, что на них нет мусора и грязи. Почистите челюсти, затем протрите их чистой тканью. | ||||
Шаг 2 — Открытые лезвияРаскройте губки болторезного станка как можно шире. | ||||
Шаг 3 — Крепко возьмитесь за губкиЛучший способ удерживать головку инструмента — это закрепить ее в тисках. Однако, если вы используете напильник для заточки, вы можете просто зажать болторез между коленями. Когда вы закончите одно лезвие, ослабьте тиски, переверните губки и повторно зажмите, чтобы взяться за следующий. | ||||
Шаг 4 — Напильник под углом… Лезвия болторезных станков, как и у ножниц, имеют фаску по краю. | ||||
Шаг 5 -… но не слишком резкий!Не шлифуйте и не подпиливайте лезвия болторезных станков до очень острых краев. У них должен быть закругленный выступ, так как им не нужно «прорезать» материал, а скорее раздвигать его.Чрезмерно острые кромки уменьшают эту тупую разделяющую силу и делают кромки лезвия уязвимыми к короблению и вмятинам. | ||||
Шаг 6 — ОчиститьПочистите, а затем протрите лезвия тканью, когда вы закончите опиливать, чтобы удалить мелкие металлические частицы, которые будут образовываться. | ||||
Шаг 7 — Нанесите масло Наконец, снова возьмите тряпку и протрите лезвия по всей длине большим слоем масла. | ||||
Как затачивать кусачки
Вам не нужно обращаться к профессионалу, чтобы заточить кусачки . Это можно сделать за считанные секунды, не выходя из дома. Прочтите, чтобы узнать, как это сделать.
Шаг 1 — Мера безопасности
Заточка кусачков требует большого мастерства.Уровни риска невысоки; это довольно просто и не требует сложных инструментов. Но прежде чем начать, убедитесь, что на вас надеты рабочие перчатки. Также надевайте защитные очки, чтобы защитить глаза.
Шаг 2 — Рабочая зонаЧтобы определить проблемные участки в кусачке, вам понадобится хороший глаз. Поэтому, чтобы облегчить процесс заточки, убедитесь, что на вашем рабочем месте достаточно света.
Шаг 3 — Инструмент Как упоминалось ранее, для заточки кусачка не требуется высокопроизводительный или сложный инструмент. Простая ручная пилка сделает свое дело.
Ручные файлы бывают разных типов. Типы распознаются по текстуре на ручных файлах. Чем грубее текстура, тем больше истощает поверхность, о которой натирают. Чтобы заточить кусачки, вам следует выбрать ручной напильник с мелкой текстурой. Если вы выберете очень грубый ручной файл, он повредит кусачки. Это связано с тем, что области, которые необходимо затачивать на фрезе, чрезвычайно малы.
Шаг 5 —руб. Теперь приступим к процессу заточки. Беритесь за одно лезвие за раз. Потрите пилкой по лезвию. Действуйте быстро, но не прилагайте слишком много усилий. Мягкое растирание сделает свое дело.
Шаг 6 — Тест После того, как вы заточите все лезвия на кусачке, вам нужно проверить его работу. Попробуйте перерезать провода инструментом. Если он выполняет свою работу без особых усилий с вашей стороны, значит, заточка прошла успешно. Если нет, вам придется его еще немного заточить.
Когда вы добьетесь нужной резкости, остановите процесс. Теперь нужно очистить лезвия. Используйте проволочную щетку для очистки лезвий, а также внутренних частей кусачка.
Шаг 8 — Техническое обслуживаниеЗаточка — это процесс, который можно повторять бесконечное количество раз, но для увеличения долговечности лезвий обязательно очищайте резак после каждого использования.Правильный уход снизит потребность в ее заточке. Следуйте этому совету, чтобы сохранить резкость. Лезвия следует очищать мыльной водой после каждого использования. Также поможет протирание лезвий спиртом.
Шаг 9 — WD40Также, прежде чем приступить к процессу заточки, если вы обнаружите, что на лезвии есть посторонние элементы, очистите их. Липкие вещества можно удалить с помощью WD40.
Шаг 10 — Хранение Последний шаг — правильно хранить фрезы. Неправильные методы хранения также приводят к потере остроты кусачки. Всегда смазывайте лезвие перед хранением в сухом месте.
Заточка бензопилы — 10 правил, которые можно и нельзя делать
Фото: istockphoto.com
Работаете ли вы на дереве или просто хотите рубить дрова своими руками, очень важно поддерживать профессиональное отношение к их использованию и использованию. обслуживание вашей бензопилы. По мере того, как десятки режущих зубов прорезывают плотную древесину, они неизбежно затупляются, снижая эффективность инструмента и делая его физически более сложным для вашего контроля.Регулярная заточка, выполняемая опиливанием, заставит вашу бензопилу мурлыкать, как очень грубый котенок. Прежде чем приступить к выполнению этой задачи, прочтите о способах и средствах правильной заточки бензопилы.
DO Изучение цепной пилы Ознакомьтесь с частями цепной пилы, изучив подробные схемы в руководстве пользователя. В дополнение к звеньям и ремешкам вы увидите множество фрез, которые составляют основу процесса заточки. Каждый резак имеет две острые области: одна на краю верхней пластины, а другая на внешней пластине, где она пересекает верхнюю пластину.В середине резака есть выемка, известная как «глотка», а на другом конце — выступ в виде крючка. Крюк, иногда называемый «граблями», представляет собой глубиномер, который определяет, насколько резцы вырезают древесину во время работы пилы. Заточка резцов бензопилы и заточка ограничителей глубины обеспечивают оптимальную резку. Имейте в виду, что форма и размер фрезы для бензопил немного различаются от модели к модели, но все отточены одинаково.
Старое правило заключалось в том, чтобы затачивать бензопилу, когда она производит больше древесной пыли, чем щепы во время работы.Более разумный ход — заточить фрезы до этой точки. Если вы будете затачивать каждый второй или третий раз, когда заправляете бензопилу топливом, процесс заточки будет минимальным, и у вас никогда не будет тупой пильной цепи.
DO Стабилизируйте бензопилу Удерживайте бензопилу в установленных тисках во время хонингования резцов. Если вы собираетесь провести весь день в лесу, подумайте о тисках, установленных на задней двери, которые позволят вам стабилизировать пилу для легкой заточки на месте.
Фото: istockphoto.com
НЕ Забудьте о защитной одеждеЦепь пилы с множеством острых ножей может поцарапать или порезать голую кожу, поэтому надевайте прочные рабочие перчатки, желательно кожаные, прежде чем ты начнешь. Вам также понадобятся хорошие защитные очки, чтобы защитить глаза от стружки.
DO Использование правильного диаметра напильникаКруглый напильник обычно используется для заточки фрез для цепной пилы, и стандартный диаметр большинства напильников, используемых для этой цели, составляет от 4 до 6 мм.Но не все пильные цепи одинакового размера. Найдите в руководстве пользователя оптимальный диаметр напильника для заточки пильной цепи.
НЕ Не оставляйте свое дело Большая часть пиломатериалов выполняется вдали от дома, поэтому не забывайте брать с собой заточные инструменты. В противном случае вы вернетесь назад, прежде чем заполните кузов дровами.
Чтобы режущая кромка была максимально острой, напиливайте ее от внутренней кромки резака к внешней кромке.Пильные цепи имеют как правые, так и левые резаки, чередующиеся от одной стороны пильной цепи к другой. Чтобы подпилить отдельные фрезы, встаньте с одной стороны пильного полотна и подпилите фрезы с противоположной стороны пильной цепи. Например, если вы стоите с левой стороны пильного полотна, вы подпилите фрезы с правой стороны пильной цепи. Когда вы закончите с одной стороной, перейдите к другой стороне пильного полотна и подпилите оставшиеся фрезы.
НЕ Потяните напильник — надавите на него Круглый напильник затачивается только в одном направлении — на ходу от вас .Чтобы заточить режущий угол (место на резце, где пересекаются острая верхняя и боковые пластины), держите файл горизонтально и следуйте заводскому углу режущего угла, слегка, но сильно нажимая на файл. Затем поднимите напильник, чтобы вернуться в исходное положение, и снова надавите на него. Используйте одинаковое количество опилов и одинаковую степень давления для подпиливания всех фрез. Для заточки режущего угла может потребоваться всего два хода на резак, но может потребоваться и больше, если резцы очень тупые.
Если вы не уверены в правильности подшивки заводских углов резака, используйте направляющую для заточки. Эти недорогие инструменты напоминают линейки и имеют в нижней части скобу, на которой находится круглый напильник. Ручные модели стоят менее 10 долларов, но если вам нужна дополнительная помощь, выберите направляющую, которая надежно фиксируется на пильном полотне. Направляющие имеют предварительно размеченные линии, которые позволяют выровнять файл под правильным углом заточки, обычно около 30 или 35 градусов.Обратитесь к руководству по эксплуатации, чтобы узнать правильный угол заточки вашей пильной цепи.
Глубиномеры также требуют подпиливания, но не так часто, как резаки. Со временем и распиловка, и опиливание сказываются на резаках, изнашивая их до тех пор, пока ограничители глубины (которые торчат впереди на каждой резце) не становятся слишком высокими. Это может сделать пиление неэффективным, потому что ограничители глубины фактически блокируют фрезы. Вы можете подпиливать от руки, прямо поперек, плоским напильником, или приобрести направляющую для ограничителя глубины, которая подходит между резцами и имеет отверстие, которое позволяет подпиливать верхнюю часть ограничителя глубины.Верхняя часть ограничителя глубины должна быть всего на волосок — 0,025 дюйма — ниже вершины режущего угла резака.
Фото: istockphoto.com
Как пользоваться болторезами как босс
Назовите меня дураком, но хороший набор прочных болторезных инструментов — это мгновенная инъекция тестостерона. Взяв в руки ручной инструмент, способный с минимальными усилиями пробивать стальные прутья, вы не можете не хотеть высвободить эту разрушительную силу при любой возможности.
Кроме того, существует основная мысль, что никакой замок не является безопасным. Не то чтобы я был сторонником взлома и проникновения, но простой факт, что пара качественных болторезных станков быстро справится с запертыми воротами, ну, концепция дает вам силы, действуете ли вы в соответствии с ней или нет.
В общем, увлекаюсь. Эта статья не имеет ничего общего с потенциальным преступным использованием болторезных станков — это простое руководство, объясняющее, как правильно использовать болторезные станки.
Зачем нужна пара болторезных станков?
В нашей обзорной статье 5 лучших болторез мы подробно рассказали о различных типах болторез и о том, почему вы должны иметь пару.Мы кратко рассмотрим это здесь. Болторез — идеальный переносной ручной инструмент, который можно использовать для разрезания замков, цепей, заборов и болтов.
Болторез можно использовать в домашних условиях. Это прочные инструменты, которые будут работать в любой ситуации, когда нужно вырезать небольшой кусок металла (обычно цилиндрической формы).
Фрезы бывают разных размеров от 8 до 42 дюймов в длину. Качество сборки зависит от используемой стали для режущей головки.Материалы ручки также различаются. (Чтобы узнать больше, прочтите наше руководство покупателя болторезных станков).
Итак, это основы работы с болторезными станками, теперь пора научиться пользоваться парой.
** Знаете кого-нибудь, кому нужен паяльный станок? Узнайте, какое устройство для стыковки печенья лучше всего подходит для вас, подробнее об этом здесь! **
Как использовать болторезные станки, как бобышку
1. Подготовка: регулировка резаков
Большинство болторезных станков поставляются с регулировочный болт, встроенный в режущую головку.Перед работой с инструментом вы должны повернуть его, чтобы установить правильное натяжение лезвий.
Это позволит вам получить желаемое натяжение, соответствующее вашему удобству работы и твердости обрабатываемого материала.
2. Подготовка: маркировка мишени
Для чистых резов в нужном месте всегда сначала следует разметить материал. Все, что вам может понадобиться — это небольшая, но четкая маркировочная линия или даже точка. По возможности следует также зажать материал, который нужно разрезать.По крайней мере, он должен быть в фиксированном положении.
3. Откройте режущие лезвия
Режущая головка и лезвия открываются, если потянуть в стороны ручки болторезного станка. Перед тем как начать, вы должны расположить лезвия как можно дальше друг от друга. Затем переместите режущую головку так, чтобы мишень оказалась в центре лезвий.
4. Позиционирование для реза
Теперь, когда мишень находится в центре лезвий, важно расположить материал как можно ближе к пересечению ручки.Как только лезвия закрыты, это точка, в которой начнется резка. Это также будет область, которая обеспечивает наибольшую силу.
5. Выполнение разреза
Теперь все, что вам нужно сделать, это закрыть ручки, чтобы сделать разрез. Медленно и крепко закройте болторез. Если ваша хватка ослаблена, ножи могут поскользнуться на материале и проткнуть металл далеко от цели.
Связанное содержание:
6. Приложение силы и наблюдение за ней
После того, как материал пробит, настало время довести разрез до конца (термин «раздавливание» на самом деле более уместен, поскольку именно это болт фрезы делаю).
После первоначального контакта между лезвиями и материалом убедитесь, что вы поддерживаете давление резания в том же месте. В некоторых случаях при работе с более прочными материалами потребуется открыть режущую головку и повторить действие. Удостоверьтесь, что вы попали в ту же точку на следующем разрезе.
Как использовать болторезные станки (видео)
>> Ищете долбежный станок? Ознакомьтесь с нашим полным руководством здесь !!! <<
Как точить инструменты
Обеспечение остроты инструментов экономит время и силы.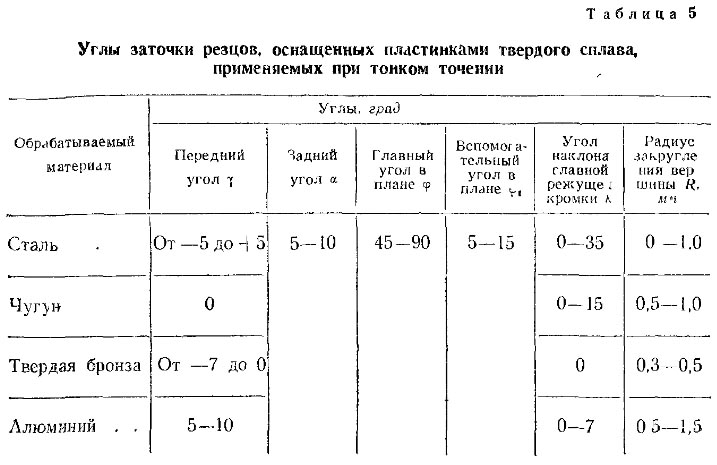
W Если вы спешите Чтобы завершить работу по обрезке, вы можете не тратить лишние несколько минут необходимо остановить и заточить ваши инструменты. Но это того стоит. две причины:
1) Ваша работа пойдет быстрее и проще с заточенными инструментами.
2) Чистый срез, получаемый с заостренные инструменты более полезны для ваших растений и деревьев.
Сразу после резки, растение сочится соком или смолой, которая при высыхании создает защитный щит.Но это только начало процесса исцеления. Завод тоже отвлекает энергия от ее роста до поврежденного участка, пока рана заживает. Очевидно, тогда вы хотите, чтобы дерево зажило так же быстро. насколько возможно. Один из способов сделать это — создать гладкую поверхность. чистым срезом с помощью заточенного инструмента. Мало того, что растение лечит больше быстро и, следовательно, быстрее начнет расти, но будет меньше подвергаться ущерб от болезней, насекомых, грибков и экстремальных погодных условий.
После этих шагов будет
поможет вам узнать правильный способ отточить инструменты для обрезки.
Шаг 1: Очистите лезвия
Любой инструмент для обрезки вы используете, очистите лезвие жесткой щеткой и мыльной водой, чтобы удалить любая ржавчина, комки грязи или другой мусор. Обмакните секатор в растворитель, например как керосин, чтобы счистить остатки сока. Если вы использовали свои инструменты для вечнозеленых растений, Не забудьте также очистить остатки смолы маслом или керосином.После высыхания протрите лезвия легким слоем моторного масла.
Шаг 2: Проверьте резкость
Осмотрите край лезвия, чтобы определить правильный угол заточки (обычно от 10 до 15 градусов) (см. фото 1, слева). Также рекомендуется ознакомиться с рекомендациями производителя. для получения более конкретных инструкций и предостережений по заточке. Помните, для секатор типа наковальни, вы будете затачивать только одно лезвие, но вы должны затачивать это лезвие с обеих сторон.
Выбор инструмента для заточки в значительной степени вопрос предпочтений:
* Брусочки самые распространенные
выбор, предложите множество градаций и размеров, хотя вы можете найти, что
с одним легче работать.
* Плоский напильник с алмазным покрытием требуется только вода для смазки, остается плоским для быстрой заточки и достаточно прочный, чтобы прослужить всю жизнь.
* Подходит для заточки стали для отделки или для быстрого ремонта.
* Шлифовальные камни требуют доп. осторожность, потому что они передают тепло от трения, которое может повлиять на состояние металла, делая его более хрупким.
Из-за использования брусков является наиболее распространенным из этих четырех типов, опишите эту технику в подробно здесь.
Шаг 3: Начните шлифование лезвия
Начните со среднезернистого точильного камня
(см. Фото 2, противоположная страница, вверху). Тщательно намочите камень, намочив
это в воде или легком моторном масле. (Для еще более светлого финиша некоторые
люди предпочитают использовать растительное масло.) Поскольку вода быстро испаряется,
масло обычно является лучшим выбором. Он не только действует как смазка, но и
уносите песчинки во время процесса заточки.
Чтобы сохранить правильный угол, при заточке прижмите лезвие к вогнутой стороне камня.Используйте множество плавных движений, перемещая лезвие в одном направлении к типо, если вы пытаетесь сбрить тонкий ломтик от точильного камня. Не давите слишком сильно.
На каждые 10 ходов до внешний скос, нанесите один ход на внутренний угол.
Периодически увлажняйте камень нанесение большего количества воды или масла. (Однако не переключайтесь между ними. Если вы начинаете с масла, продолжайте использовать масло.)
Если на лезвии есть зазубрины, используйте напильником для удаления погнутой металлической детали. Если у него несколько ников, вы можете начинать процесс заточки нужно с более грубого камня.
Шаг 4. Сгладьте края
Как только вы добьетесь нужного
угол и резкость, перейдите к использованию точильного камня с более мелким зерном и продолжайте
затачивайте до тех пор, пока не получите острый край. Не уменьшайте скошенный
кромка толщиной менее 1 мм. Более тонкая кромка не приведет к увеличению резкости
но сделает лезвие более хрупким и подверженным повреждениям или поломке.
Шаг 5: Проверьте резкость
Можно провести предварительную проверить, не выезжая на улицу.Просто держитесь за режущий край до источника света. Если вы видите свет, отражающийся от края лезвия, его еще недостаточно заточено.
Как только инструмент проходит через отражение света test, вы готовы к окончательному тесту, попробовав его на размере ветки он предназначен для резки (см. Фото 3, справа посередине). Если вы заточены лезвия правильно, они будут делать чистые, легкие разрезы. Если лезвия тянут или поймать, они недостаточно острые. В этом случае продолжайте заточку с точильный камень или переключитесь на сверхтонкий камень.При необходимости повторите тест, снова будьте осторожны, чтобы не переточить лезвия.
Шаг 6: Добавьте слой масла
Обработать лезвия потиранием.
слегка смажьте их маслом (см. Фото 4, справа внизу). Помните: грязь, которая
прилипает к вашим инструментам, действует как губка, собирая влагу и вызывая
ржавчина. Поэтому убедитесь, что ваши инструменты не загрязняются, когда они не используются.
При заточке других типов инструментов, вам может потребоваться внести некоторые изменения в эти шаги. Например, при заточке секаторов или ножниц типа наковальни затачивайте только одно лезвие но с обеих сторон.Избегайте изгиба кромки лезвий. Если только край идеально ровный, он не ударится о плоскую наковальню, и пряди растительной ткани будут цепляться за лезвие после каждого разреза.
Перед заточкой ножниц вы может оказаться проще их разобрать. Помните, что переточка лезвий обычно не рекомендуется. Это приводит к изменению угла резания. и уничтожить гофру. Кроме того, переточка может создать выпуклую режущую кромку. что приводит к плохому стригущему эффекту и затруднению резания.
Для «обхода» ножничного действия
срезные ножницы затачивайте только внешнюю поверхность каждого лезвия. Это будет
поддерживайте режущую поверхность, чтобы лезвия шли чисто при скольжении
мимо друг друга. Помните, что внутренние поверхности лезвия должны оставаться
плоские, поэтому их следует чистить, но не затачивать.
При заточке инструменты, также неплохо проверить натяжной винт между лезвиями. При необходимости отрегулируйте винт, чтобы обеспечить большую свободу движений в неподвижном состоянии. убедитесь, что лезвия расположены достаточно близко друг к другу для правильной работы.
Что делать, если у вас есть пила, нужна заточка? Это утомительная работа, требующая особых навыков и особых оборудование, так что вы, скорее всего, захотите доверить это профессионалу. Проверять Желтые страницы в разделе «Услуги по заточке» или посетите местный хозяйственный магазин.
После заточки инструмента
несколько раз вы можете заметить, что угол резания становится скругленным
(кромка под углом более 90 градусов). На этом этапе лезвия
начните работать с дробящего действия вместо отсечения. Этот
указывает, что лезвие изношено, и пришло время заменить его или весь
инструмент.
Защитите свои вложения в качественные инструменты и ограничивают потребность в заточке, выполняя плановое обслуживание между использованиями. Найдите удобное и легкодоступное место, чтобы повесить тряпку. сухой с одной стороны и масло с другой. Используйте его, чтобы стереть свои инструменты, держать их в чистоте и смазывать после того, как вы закончите их использовать. Это особенно важно выполнить эту небольшую задачу, прежде чем убирать инструменты для время года.
Еще один удобный прием — сохранить
ведро на 5 галлонов, заполненное крупным строительным песком в вашем гараже или в инструменте
пролить. Окуните металлические лезвия каждого инструмента в песок и потяните их вверх.
и вниз несколько раз. Это удалит грязь или прилипшую землю. Следующий,
используйте металлическую щетку или стальную вату, чтобы удалить ржавчину и другие частицы
остатков мусора. Также можно в ведро налить немного моторного масла. песка так, чтобы, окунув их в песок, чтобы очистить, вы дали
их слой масла.
Несмотря на эти рекомендации,
если вы по-прежнему не смазываете инструменты регулярно, по крайней мере, делайте это в
в конце сезона, нанеся легкий слой масла на лезвия.Также защитите
инструменты с деревянной ручкой, смоченные льняным маслом или слоем лака. И смазать
любые движущиеся части. Затем храните инструменты в сухом месте. Следуя этим шагам,
Ваши инструменты будут готовы в любое время и в любое время года.
Заточка фрезы вручную — Simple Works Best
Я еще никогда не видел выемки для машинной резки с такой же безупречной поверхностью, как наконечник для копья (я уверен, что они есть, но не такие доступные, как резаки для копья), но его нужно настроить вверх и правильно заточен.
Мне нравятся простые, необычные, неинвазивные методы повышения резкости, о чем знает большинство из вас, читающих мой блог и смотрящих мои видео. Простые вещи, простые системы, которые совсем не просты, но работают эффективно и результативно. Поэтому я стараюсь найти их — не только для себя, но и для вас тоже. Вопрос о фрезерных фрезах и о том, как их затачивать (не фрезерные станки, а фрезы ручные фрезерные) возникает достаточно часто, чтобы показать, что большинству людей сложно добиться хорошей острой и квадратной кромки для них, не без борьбы .Если у вас суперсильные пальцы, это не проблема, и я имею, но если у вас нет шансов, вы создадите двунаправленный изгиб к скосу, и это создаст проблему для создания режущей кромки параллельно или копланер к подошве самолета. В результате получается неровная или слегка ступенчатая поверхность над фрезерованной выемкой. Для большей части работы, которую мы выполняем, это может быть не так важно, но когда мы хотим, чтобы выемка была как можно более безупречной, это возможно.
Если вам нужно знать, как установить положение режущего инструмента параллельно подошве, перейдите к серии на плоскости фрезерования, которая включает настройку для идеальной отделки поверхности выемки. Это одна из тех, над которыми я действительно работал, разработал и использовал большую часть содержания для моей последней книги, Основные инструменты для деревообработки . При разработке фаски люди чаще всего ошибаются, поэтому я разработал другой метод заточки, который работает для получения острых кромок, а также работает для поддержания скоса резки под прямым углом к кромке, чтобы скос не подорвал работу, которую вы проделали при разработке параллелизма фрезы к подошве. Я, возможно, мог бы подумать о включении в свою книгу, но здесь это сработает, чтобы рассказать людям об этом.
Метод, который я сейчас рекомендую, пришел из моей работы по установлению и поддержанию правильного угла для заточки лезвия ножа. Регулируя высоту «стола» с помощью тисков, вы эффективно определяете желаемый скос в зависимости от выполняемой работы. При подъеме стола скос становится круче, при опускании стола скос становится меньше. Это очень просто и очень эффективно. Хотя мой процесс заточки ножей эволюционировал на протяжении многих лет, лучшим, но все же был последний, о котором я опубликовал в блоге выше в начале января этого года.
Сначала я создал ступеньку, просто выпилив ступеньку, как показано. Я снял фаску на прилегающей более высокой поверхности, чтобы острый хон мог получить доступ по всей фаске без споткнуться. Фактически вы можете создать вторую ступеньку под углом для заточки резцов с наконечником на той же платформе. Первый шаг вниз предназначен для квадратных фрез и действует как упор, чтобы подтолкнуть фрезу и зафиксировать ее. Поместив фрезу с лезвием, выступающим всего на мил или два, хонингование упрощает заточку этих неудобных резцов независимо от их марки.Готовясь к нескольким лекциям на выходных, я идеально затачил фрезы шести различных марок без каких-либо препятствий. Заточка фрезы с острием копья просто означает использование той же ступеньки со скосом, но с поворотом опоры для выполнения второго скоса в противоположную сторону.
Расстояния
—— Поскольку скольжение хона по столешнице умеренно изменчиво, так что вы используете всю поверхность алмазного хона, фаска фрезы имеет очень небольшой и почти незаметный изгиб, который, на мой взгляд, идеален.Я использую круговые движения без жидкости, и это прекрасно работает, потому что при необходимости вы можете легко смыть или стереть стружку. Установите платформу на 62 мм (2 1/2 дюйма) над столешницей так, чтобы верхний край платформы был параллелен скамейке. Лучше и проще всего провести линию поперек платформы 62 мм. После того, как фаска определена с помощью этого метода, потребуется всего несколько секунд для ее дальнейшего уточнения, при этом другие параметры шлифовки будут переходить от среднего к тонкому, а затем к сверхтонкому. Я даже увеличил свой до 10 000 полировальной пастой на кожаном ремешке, так как это так мало, чтобы пройти лишнюю милю.
Похожие сообщения3 способа заточки наконечника одностороннего резака Система Easy-Core Coring
Наконечник резца для системы OneWay Easy-Core Coring System — это мощная режущая машина, которую необходимо часто затачивать.
Как затачивать наконечник OneWay Easy-Core Cutter?
Есть несколько способов заточить резак OneWay Easy-Core Cutter. Вы можете заточить вручную алмазным шлифовальным станком, или есть несколько способов заточить Easy-Core Cutter на станции заточки.
Как не точить односторонний резак
Возможно, вы посмотрели на резак, установленный на кронштейне ножа в системе одностороннего бурения, и подумали: «Я могу просто оставить резак в ноже и перенести нож целиком на точилку».
Это не сработает, к тому же вам нужно будет заточить установочный винт, чтобы заточить верхнюю поверхность фрезы.
Но не волнуйтесь, вы не одиноки, я тоже думал об этом сам. Есть лучшие способы заточить кончик фрезы, продолжайте читать.
В этой статье я расскажу вам о трех различных способах заточки наконечника OneWay Easy-Core Cutter.
Частота заточки режущих кромок
Если острие ножа затупилось, потребуется большее усилие на нож для вырезания керна. Дополнительное давление может привести к отклонению и изменению траектории ножа и сделать траекторию резания шире, чем необходимо.
Наконечник системы Easy-Core Coring System — это рабочая лошадка всей системы отбора керна, и она должна оставаться острой.
Каждая древесина индивидуальна, и лезвие фрезы затупится с разной скоростью.
Я обнаружил, что сухая древесина твердых пород может плохо повредить наконечник фрезы. Иногда наконечник резака может потребоваться несколько раз для заточки всего лишь одного среза чаши для удаления сердцевины.
С другой стороны, зеленая мокрая древесина может быть мечтой, чтобы отделить ее. Я обработал сердцевиной несколько заготовок из зеленой вишни, и мне нужно было только один раз переточить кончик резака OneWay Cutter.
Когда точить
Если вы заметили, что нож OneWay Coring не так быстро входит в проход резки, возможно, пришло время заточить кончик резака.
Еще один признак того, что режущий конец необходимо затачивать, — это размер пыли и стружки.
Резка, выполняемая резаком OneWay Easy-Core Cutter, представляет собой гибридную очистку и резку. С острым режущим лезвием вы, вероятно, увидите пыль с торцевых областей волокон и некоторые фигурные стружки от боковых разрезов, в зависимости от древесины.
Когда режущее лезвие затупляется, при резке образуется более мелкая пыль, а боковые срезы также могут измениться от стружки до пыли.
Если вы видите, что из отверстия для керна выходит дым, скорее всего, необходимо немедленно заточить наконечник фрезы и уменьшить силу, используемую для выполнения резки, скорость токарного станка или давление на рукоятке, или и то, и другое.
Перед тем, как заточить режущий наконечник
Резак OneWay Easy-Core Cutter необходимо снять с режущего ножа, прежде чем его можно будет заточить.
Верхняя поверхность фрезы должна быть гладкой, и выступающий шестигранный винт будет мешать процессу заточки.
Осторожно снимите шестигранный винт с режущей головки с помощью шестигранного ключа и поместите его на магнит или магнитный лоток. Этот винт довольно маленький, и если его уронить на пол, покрытый стружкой, его легко потерять.
Также рекомендуется удалить пыль с лезвия ножа системы OneWay Coring System и самого отверстия для винта. Это обеспечит правильную посадку режущего конца при его возврате.
Держите под рукой емкость с водой, чтобы охладить фрезу, так как она может нагреваться во время процесса заточки.
Заточка резака OneWay вручную
Самый быстрый и простой способ заточки наконечника OneWay Easy-Core Cutter — вручную с помощью простой алмазной шлифовальной карты.
Проблема с заточкой или хонингованием вручную, и это в точности. При ручном хонинговании может быть непросто выдержать углы и кромки режущего инструмента, указанные производителем.
Чтобы избежать слишком большого количества разнонаправленных движений, поместите алмазный шлифовальный круг на плоскую поверхность. Плоская поверхность сохраняет устойчивость одной стороны уравнения.
Вы не хотите, чтобы хонка была одной рукой, а кончик фрезы — другой. Это создаст несколько движений органической жидкости, и в результате получатся изогнутые поверхности вместо острых и четких фацетов.
Что требует заточки
Есть только три поверхности, требующие внимания: плоская верхняя поверхность и две скошенные кромки острия фрезы.
Нет необходимости затачивать какие-либо другие участки наконечника фрезы OneWay, потому что надрезы производятся только верхушкой и острым наконечником.
Я упомяну об этом, потому что это есть в инструкции, но это кажется довольно очевидным. Канавки в нижней части фрезы НЕ затачиваются. Они должны оставаться такими, как есть, потому что они захватывают и сцепляются с поверхностью режущего ножа.
Заточка вручную
Установите алмазное хонингование на плоскую поверхность и начните с хонингования плоской верхней поверхности фрезерной головки. Плавными плавными движениями переместите фрезу вверх дном по алмазной головке.
Когда вся верхняя поверхность резака OneWay станет чистой и гладкой, можно переходить к заостренному стрелой наконечнику.
Заостренный наконечник — самая сложная часть процесса заточки. Не торопитесь и расположите руку так, чтобы каждый острый угол был заподлицо с поверхностью алмазной шлифовки.
Отрегулируйте положение до тех пор, пока скошенная поверхность наконечника фрезы не станет плоской на хонингере. Просто совместите существующие углы на кончике фрезы.
Рекомендуется положить запястье на плоскую поверхность, чтобы стабилизировать и поддерживать движения вперед и назад.
Перемещайте режущую головку вперед и назад, пока каждый скос не станет снова чистым и хрустящим.
Хотя эта техника ручной заточки будет работать, поддерживать постоянство непросто. Когда я это сделал, со временем углы режущего лезвия немного сместились, и плоские режущие поверхности стали скорее округлыми, чем плоскими.
Потеря угла режущей кромки
Со временем углы режущего конца режущего инструмента могут немного смещаться и изменяться, а может и хуже.
Углы скоса наконечника должны составлять 45 ° сверху вниз, а острие стрелки состоит из двух углов по 20 °, которые пересекаются посередине.
Конечно, как и многочисленные потенциальные углы заострения чаши, они не должны быть точными, но, вероятно, не должны сильно отклоняться.
Можно ли затачивать фрезы OneWay Easy-Core на круге из CBN?
Да, резак можно затачивать на круге из CBN вручную или с помощью приспособления для заточки резцов OneWay Easy-Core Cutter Sharpening Jig.
Заточный нож на колесе ручной
Второй способ заточки резца системы Easy-Core Coring System — использовать заточный диск на станции заточки и держать наконечник резца рукой.
Из-за небольшого размера острия фрезы контакт с точильным кругом немного нервирует. Если эта идея не для вас, перейдите к следующему способу заточки резака или попробуйте схватить кончик резака плоскогубцами.
Для заточки круга вручную необходимо установить платформу для заточки под углом, который наилучшим образом соответствует угловым скосам на наконечнике фрезы.Отрегулируйте платформу заточки перед включением болгарки.
Используйте самый лучший точильный круг, который у вас есть. Я использую круг из CBN с зернистостью 180 для заточки режущих пластин OneWay Easy-Core.
Убедитесь, что платформа находится как можно ближе к точильному диску. Любой зазор может позволить резцу зацепиться и направить наркотик вниз.
Будьте осторожны с точильным кругом
Очевидно, на всякий случай наденьте все защитное снаряжение (защитные очки, перчатки, маска для лица — тоже неплохая идея).
Также носите пылезащитный чехол с пылезащитными фильтрами 3M 2097, потому что металлическая стружка от вашей системы заточки намного опаснее, чем вы можете себе представить.
Не торопитесь и осторожно опустите режущие поверхности одну за другой, чтобы они соприкасались с поверхностью заточного круга. Делайте только короткие легкие прикосновения и часто проверяйте поверхность.
Достаточно лишь пары легких прикосновений к диску, чтобы восстановить кромку фаски фрезы. Будьте осторожны, чтобы не резать слишком долго или слишком сильно, потому что вы можете быстро изменить форму всего резца, слишком долго затачивая.
Шаблон для заточки резцов Easy-Core Cutter
Третий и текущий способ заточки резца OneWay — это приспособление для заточки резца Easy-Core Cutter.
Когда я сказал, что помогу вам узнать все, что знаю о токарной обработке деревянных чаш, я имел в виду именно это. Видите ли, теперь вы знаете два способа, которые вроде бы работают, и вам не нужно проходить все эти шаги, если вы не хотите. Ха!
Безусловно, самый простой способ заточить эту маленькую режущую головку OneWay — это использовать приспособление для заточки резцов Easy-Core Cutter Sharpening Jig.Приспособление действует как держатель и направляющая, чтобы удерживать режущую головку, когда вы приводите ее в контакт с заточным кругом.
Использование приспособления для заточки резцов Easy-Core Cutter
Еще одна веская причина использовать это приспособление — это то, что он поставляется с шаблоном угловой платформы. Выключив шлифовальный станок, установите платформу с помощью прилагаемого углового шаблона, и платформа будет установлена. Не нужно гадать или суетиться.
Заточный приспособление поставляется с дополнительным более коротким винтом, который не мешает вставлять в наконечник резака.Таким образом, верхняя поверхность фрезы будет четко видна и готова к плавной заточке.
Первый проход заточки
Используйте шаблон платформы с меньшим углом, который составляет 90 °, чтобы отрегулировать платформу для заточки на 90 °. Это будет угол, необходимый для заточки верхней поверхности фрезы.
Когда режущая головка прикреплена к зажимному приспособлению, положите зажимное приспособление боком на платформу и слегка коснитесь токарного заточного круга, чтобы сгладить верхнюю поверхность.
Второй проход для заточки
Затем используйте шаблон 45 ° или больше, чтобы отрегулировать платформу на 45 °.Опять же, положив кондуктор на бок на платформе, поднесите заостренный конец фрезы к точильному диску.
Угол платформы учитывает подрезку под углом 45 °, но вам нужно будет приблизительно определить два угла 20 °, образующих острие.
Осторожно прикоснитесь к кругу, пока одна сторона не окажется под углом 20 °, и заточите поверхность гладкой и чистой. Затем поверните приспособление в сторону на противоположный угол и повторите угол 20 ° с другой стороны.
Полная заточка
Когда резак OneWay станет чистым, блестящим и гладким, осторожно верните его в соответствующие канавки на режущем ноже.
Закрепите резак на месте шестигранным винтом и затяните винт шестигранным ключом.
Вы должны заметить более естественный и гладкий срез после того, как вернете острую режущую головку к ножу для резки кернов OneWay.
По своему опыту могу заверить вас, что частая заточка фрезы OneWay имеет важное значение в процессе удаления керна заготовок чаши с помощью системы OneWay Easy-Core Coring System.
На самом деле, как часть моей настройки перед пробивкой деревянных чаш с помощью системы одностороннего бурения, я заранее затачиваю все режущие кромки, чтобы они были загрунтованы и готовы к резке на сто процентов.
Заточку можно производить вручную с помощью простого алмазного хонинговального станка или, что более точно, с помощью специального приспособления для заточки. В любом случае, держите резак острым, и процесс удаления керна будет проходить гладко.
Ознакомьтесь с Руководством по рекомендованному бурению керна для получения полного списка всех продуктов Oneway Easy-Core Coring System.
Чтобы понять, как правильно выбрать размер и приобрести нужные детали системы одностороннего бурения Easy-Core Coring System для вашего токарного станка, обязательно прочтите эту статью.
Для получения всех подробностей о заготовках барабана для удаления керна с этой системой прочтите эту полную иллюстрированную статью Как использовать систему OneWay Easy-Core Coring system.
БОНУС: Чтобы узнать о дополнительном трюке с заточкой кончика резца в одну сторону, ознакомьтесь с тем, что я узнал от Гленна Лукаса в этой статье.
Острые инструменты имеют решающее значение для токарной обработки дежи.